Znaczenie analizy przyczyn i skutków awarii
Zastanawiasz się, w jaki sposób firmy zapewniają, że ich produkty i procesy działają bez większych problemów? Cóż, używają czegoś zwanego FMEA. Zatem FMEA oznacza analizę trybu awarii i skutków. Wiele firm używa go do wykrywania i zapobiegania problemom, zanim one wystąpią. Jeśli chcesz kopać głębiej, czytaj dalej ten przewodnik. Przyjrzyjmy się bliżej czym jest FMEA, łącznie z jego różnymi typami. Kontynuując czytanie, dowiesz się także, jak to działa i jak z niego korzystać. Wreszcie odkryj najlepszego twórcę FMEA.
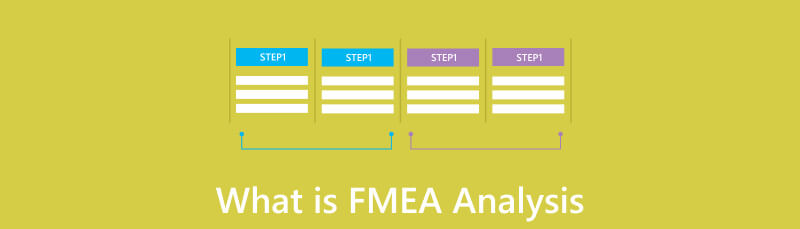
- Część 1. Definicja FMEA
- Część 2. Rodzaje FMEA
- Część 3. Jak działa FMEA
- Część 4. Jak korzystać z FMEA
- Część 5. Najlepsze narzędzie do przeprowadzania analizy FMEA
- Część 6. Często zadawane pytania na temat tego, czym jest analiza FMEA
Część 1. Definicja FMEA
Co to jest FMEA? FMEA oznacza analizę trybów i skutków awarii, często nazywaną analizą drzewa. Służy do oceny potencjalnego ryzyka związanego z różnymi trybami, w których komponent może ulec awarii. Identyfikuje także konsekwencje tych niepowodzeń i tworzy ramy umożliwiające zmniejszenie ryzyka, jeśli jest to wymagane. Inną rzeczą jest FMEA, która jest powszechnie stosowana jako ocena inżynierska. Prowadzi ją zróżnicowany zespół ekspertów. Dokładnie badają projekty produktów lub procesy produkcyjne na wczesnych etapach rozwoju. Celem tej analizy jest wykrycie i wyeliminowanie słabych stron produktów, zanim trafią one w ręce klienta. Jednocześnie zapewnia wyższą jakość i bezpieczeństwo produktu.
Spójrz na przykład analizy FMEA. Jednocześnie w trakcie pracy sprawdź, jak powstaje prezentacja wizualna.
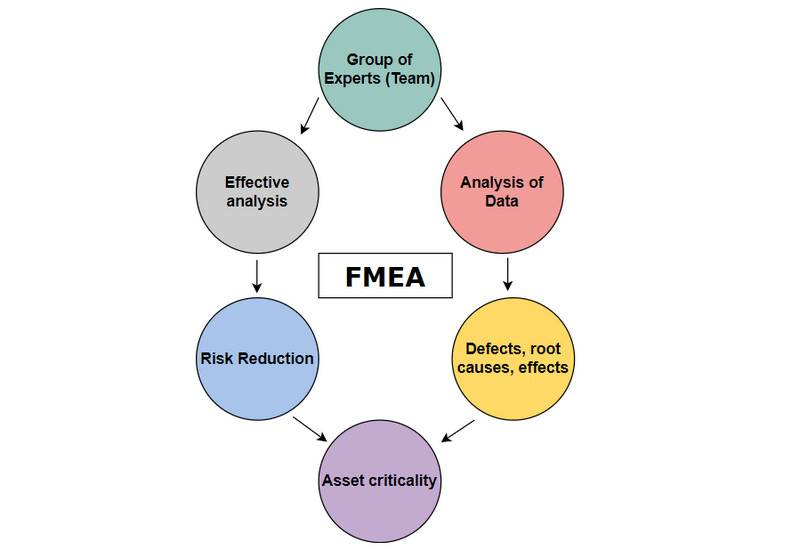
Uzyskaj szczegółową analizę FMEA.
Część 2. Rodzaje FMEA
Teraz, gdy masz już definicję FMEA, przejdziemy do jej różnych typów. FMEA ma trzy główne typy, każdy z nieco innym celem. Poznaj te typy, czytając dalej poniżej:
1. Projekt FMEA (DFMEA)
Projektowanie FMEA koncentruje się bardziej na systemie lub produkcie na etapach planowania i projektowania. Zespoły w DFMEA starają się znaleźć i naprawić wszelkie potencjalne problemy w projekcie produktu. Zawiera części, które mogą łatwo się zepsuć, lub funkcje, które mogą być mylące dla użytkowników. Rozpoczynając analizę FMEA projektu, najpierw tworzysz listę wszystkich różnych części swojego produktu. Lista ta może być bardzo szczegółowa i zawierać wszystkie małe elementy. Po podzieleniu produktu na części należy określić potencjalne awarie każdego komponentu. Celem tego typu jest zapewnienie od początku bezpieczeństwa, niezawodności i łatwości użytkowania produktu.
2. Proces FMEA (PFMEA)
Proces FMEA polega na analizowaniu i utrzymywaniu sposobu, w jaki rzeczy są wykonywane. W PFMEA jest to wykonywane w procesie, w przeciwieństwie do DFMEA, który działa na samym produkcie. Ponadto w początkowych kolumnach arkusza PFMEA należy wymienić etapy procesu. W porównaniu do komponentów Twojego produktu w DFMEA. Tutaj zespół koncentruje się na poszukiwaniu problemów w procesach serwisowych lub produkcyjnych. Próbują ustalić, jak prawdopodobne są te problemy i jak poważne mogą być. Następnie wymyślają sposoby zapobiegania im lub naprawiania ich.
3. FMEA systemu (SFMEA)
Jak sama nazwa wskazuje, SFMEA koncentruje się na problemach związanych z systemem. Nazywa się go również funkcjonalnym FMEA lub FFMEA. Zatem ta analiza ocenia cały system bardzo wysoko. Zespoły w SFMEA analizują interakcje i połączenia między różnymi częściami lub systemami. Chcą zrozumieć, jak awaria jednej części może wpłynąć na cały system. Muszą także wiedzieć, jak zminimalizować to ryzyko. Innymi słowy, System FMEA zapewnia, że wszystkie części dobrze ze sobą współpracują w większych procesach lub projektach.
Część 3. Jak działa FMEA
Zidentyfikuj, co może pójść nie tak
Najpierw zbiera się zespół, aby sporządzić listę wszystkich rzeczy, które mogą pójść nie tak. Może dotyczyć procesu, produktu lub systemu. Bez względu na to, jak małe lub duże są błędy lub wpadki, identyfikujesz je wszystkie.
Oceń powagę
Jeśli mogą wystąpić potencjalne problemy, zespół zastanawia się i ocenia, jak poważne mogą być. Przydzielają także każdemu problemowi ocenę, która pokazuje, jak poważny jest problem. Pomaga im to w ten sposób skupić się na najważniejszych problemach.
Zdecyduj o prawdopodobieństwie
Teraz zespół oblicza prawdopodobieństwo wystąpienia każdego problemu. Zespół użyje oceny, aby oszacować prawdopodobieństwo wystąpienia takiego zdarzenia. Pomaga w ten sposób ustalić priorytety, na co należy zwrócić uwagę.
Ustal przyczyny
W przypadku każdego problemu zespół próbuje dowiedzieć się, dlaczego może się tak zdarzyć. Zespół szuka głównej przyczyny, na przykład awarii samochodu (np. niski poziom oleju).
Ustal metody zapobiegawcze
Mając wszystkie informacje, zespół przeprowadzi burzę mózgów dotyczącą pomysłów, jak zapobiec tym problemom. Jednocześnie tworzą strategie lub plany. Jednym z przykładów jest regularne sprawdzanie poziomu oleju, aby uniknąć awarii samochodu.
Dokonaj ponownej oceny i udoskonalaj
Wreszcie zespół będzie z czasem monitorował sytuację. Następnie sprawdzają, czy działania zapobiegawcze działają. Jeśli pojawiają się nowe problemy lub stare nie ulegają poprawie, wracają do deski kreślarskiej. Od tego momentu wprowadzą ulepszenia.
Część 4. Jak korzystać z FMEA
Korzystając z analizy trybów i skutków awarii (FMEA), możesz stworzyć plan bezpieczeństwa, aby zapobiec problemom. Oto prosty przewodnik dotyczący korzystania z FMEA:
1. Zbierz drużynę
Najpierw zbierz grupę ludzi. Twój zespół musi znać proces, produkt lub system, który chcesz analizować.
2. Zidentyfikuj możliwe problemy
Na tym etapie zacznij od wyszczególnienia wszystkich rzeczy, które mogą pójść nie tak. Wymień i zidentyfikuj problemy, które mogą wystąpić.
3. Oceń problemy
W przypadku każdego wymienionego problemu zastanów się, jak źle by to było, gdyby wystąpiło. Użyj skali od 1 do 10, gdzie 1 oznacza nie tak źle, a 10 jest naprawdę, bardzo źle. Pomoże Ci to ustalić, które problemy są najpoważniejsze.
4. Oceń możliwość
Następnie oszacuj prawdopodobieństwo wystąpienia każdego problemu. Każdemu problemowi przypisz ocenę możliwości.
5. Wykryj przyczyny
Spróbuj dowiedzieć się, dlaczego każdy problem może wystąpić. Jeśli martwisz się użyciem przeterminowanych składników, przyczyną może być to, że nie sprawdziłeś dat ważności.
6. Przemyśl działania zapobiegawcze
Teraz przeprowadź burzę mózgów, jak zapobiec tym problemom lub sprawić, że będą mniej groźne.
7. Oblicz priorytet ryzyka
Pomnóż wynik powagi przez wynik prawdopodobieństwa dla każdego problemu. Daje to „numer priorytetu ryzyka” lub RPN. Im wyższy RPN, tym pilniejsze jest uporanie się z tym problemem.
8. Skoncentruj się na wysokich RPN
Zwróć szczególną uwagę na problemy z najwyższymi RPN. To właśnie one wymagają natychmiastowych działań.
9. Wdrażaj i monitoruj
Wprowadź swoje działania zapobiegawcze w życie. Obserwuj rzeczy, aby sprawdzić, czy działają. Jeśli problemy nadal występują, dostosuj swój plan i spróbuj czegoś innego.
10. Regularnie przeglądaj i ulepszaj
FMEA nie jest sprawą jednorazową. Z czasem przeglądaj i ulepszaj swój plan. Gdy nauczysz się więcej, możesz uczynić to jeszcze lepszym.
Część 5. Najlepsze narzędzie do przeprowadzania analizy FMEA
MindOnMap to najwyższej klasy kreator FMEA (analiza trybów i skutków awarii). Oferuje potężną i łatwą w obsłudze platformę dla firm i organizacji. Jest to także najlepsze narzędzie do poszukiwania doskonałości w zarządzaniu ryzykiem i doskonaleniu jakości. Dzięki MindOnMap znajdziesz kompleksowe rozwiązanie zaprojektowane w celu uproszczenia i usprawnienia procesu FMEA. Tym, co wyróżnia MindOnMap jako najlepszego kreatora FMEA, jest jego intuicyjny interfejs. Zarówno początkujący, jak i profesjonaliści mogą cieszyć się z korzystania z tego narzędzia. Co więcej, zapewnia płynną współpracę zespołów. Dzięki temu każdy może wnieść swoją wiedzę i spostrzeżenia.
Teraz, niezależnie od tego, czy identyfikujesz potencjalne tryby awarii, oceniasz ich skutki itp., MindOnMap zapewnia wskazówki potrzebne do osiągnięcia doskonałości. Dzięki niemu będziesz mieć pewność, że możesz proaktywnie reagować na ryzyko, podnosić jakość produktów i optymalizować wydajność operacyjną. Dlatego jest to doskonały wybór dla osób pragnących osiągnąć doskonałość w analizie FMEA.
Bezpieczne pobieranie
Bezpieczne pobieranie

Dalsza lektura
Część 6. Często zadawane pytania na temat tego, czym jest analiza FMEA
Jakie jest 5 kroków procesu FMEA?
Pięć kroków procesu FMEA to:
1. Zidentyfikuj możliwe problemy.
2. Oceń powagę tych problemów.
3. Oszacuj prawdopodobieństwo wystąpienia problemów.
4. Znajdź przyczyny tych problemów.
5. Opracuj plany zapobiegania problemom lub zarządzania nimi.
Jaki jest przykład FMEA?
Rozważmy przykład FMEA w kontekście procesu produkcji samochodu: Najpierw zidentyfikuj potencjalne problemy, takie jak przegrzanie silnika i wady lakieru. Następnie oceń ich powagę i prawdopodobieństwo. Następnie poszukaj przyczyn, takich jak uszkodzony termostat lub błąd ludzki. Teraz opracuj plany, takie jak ulepszenia projektu i lepsza kontrola jakości. W ten sposób zapobiegniesz tym problemom i ustalisz priorytety działań.
Czy FMEA to Lean czy Six Sigma?
FMEA jest narzędziem powszechnie stosowanym w ramach metodologii Six Sigma. Nie jest to konkretnie część Lean czy Six Sigma. Jednak często jest ono włączane do tych podejść do poprawy jakości.
Wniosek
Podsumowując, poznałeś definicję i rodzaje Analiza FMEA, jak to działa i jak z niego korzystać. Rzeczywiście FMEA odgrywa zasadniczą rolę w poprawie jakości, niezawodności i bezpieczeństwa produktów w różnych branżach. W miarę jak organizacje poszukują skutecznych rozwiązań FMEA, MindOnMap wyróżnia się jako jeden z najlepszych twórców FMEA. Dzięki prostemu interfejsowi i zaawansowanym funkcjom użytkownicy mogą mieć pewność, że będą w stanie stworzyć pożądany diagram FMEA.