Significance of Failure Mode and Effects Analysis
Are you wondering how companies ensure their products and processes work without any big problems? Well, they use something called FMEA. So, FMEA stands for Failure Mode and Effects Analysis. Many companies use it for spotting and stopping issues before they happen. If you want to dig deeper, keep reading this guide. Let's take a closer look at what FMEA is, including its different types. Also, learn how it works and how to use it as you continue reading. Finally, discover the top FMEA maker.
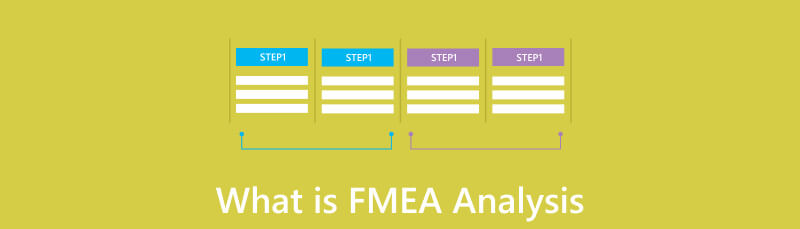
- Part 1. FMEA Definition
- Part 2. Types of FMEA
- Part 3. How Does FMEA work
- Part 4. How to Use FMEA
- Part 5. Best Tool for Doing FMEA Analysis
- Part 6. FAQs About What is FMEA Analysis
Part 1. FMEA Definition
What is FMEA? FMEA means Failure Mode and Effects Analysis, which is often referred to as Tree Analysis. It is used to evaluate the potential risks linked to various modes in which a component might fail. Also, it identifies the consequences of these failures and creates a framework to reduce risks when required. Another thing, FMEA is commonly used as an engineering assessment. A diverse team of experts conducts it. They closely examine product designs or manufacturing processes during the early stages of development. The purpose of this analysis is to detect and address the weaknesses of the products before they reach the customer’s hands. At the same time, it also ensures higher quality and safety of the product.
Take a look at an example of an FMEA analysis. At the same time, check out how the visual presentation is created as you proceed.
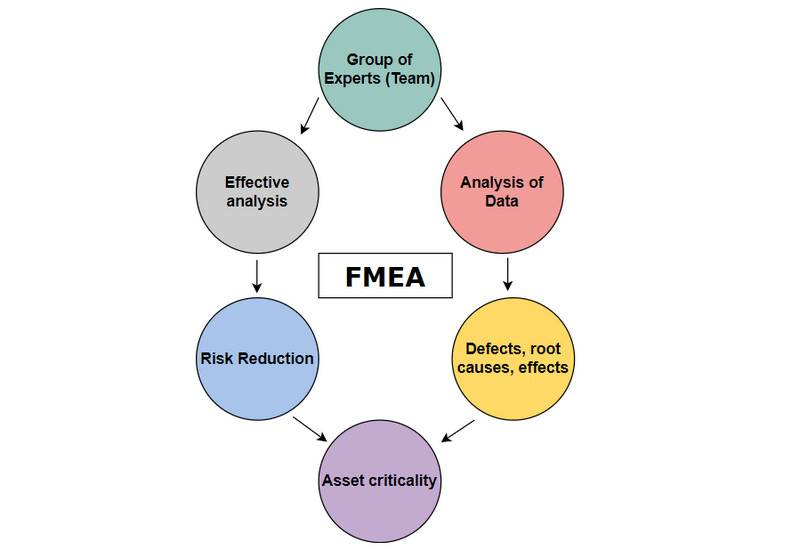
Part 2. Types of FMEA
Now that you have the FMEA definition, we’ll move on to its different types. FMEA has three main types, each with a slightly different focus. Get to know these types as you continue reading below:
1. Design FMEA (DFMEA)
Design FMEA is more focused on the system or product while in the planning and design stages. Teams in DFMEA try to find and fix any potential issues in the product’s design. It includes parts that might break easily or features that could be confusing to users. When you start a Design FMEA, you first make a list of all the different parts of your product. This list can be very detailed, with all the small pieces included. Once the product is broken down into parts, determine the potential failures of each component. The goal of this type is to ensure the product is safe, reliable, and easy to use from the beginning.
2. Process FMEA (PFMEA)
Process FMEA is about analyzing and maintaining how things are done. In PFMEA, it is performed on a process, unlike DFMEA, which works on the product itself. In addition, in the initial columns of the PFMEA Worksheet, you have to list the steps of your process. In comparison to the components of your product in the DFMEA. Here, the team focuses on searching for problems in the service or manufacturing processes. They try to figure out how likely these problems are and how bad they could be. Then, they come up with ways to prevent or fix them.
3. System FMEA (SFMEA)
As the name implies, SFMEA is focused on the system-related problems. It is also called a functional FMEA or FFMEA. So, this analysis looks at the whole system highly. Teams in SFMEA analyze the interactions and connections between different parts or systems. They want to understand how a failure in one part could affect the whole system. Likewise, they have to know how to minimize those risks. In other words, System FMEA ensures that all the parts work well together in larger processes or projects.
Part 3. How Does FMEA Work
Identify What Could Go Wrong
First, a team gathers to make a list of all the things that might go wrong. It could be in the process, product, or system. No matter how small or big the mistakes or mishaps, you identify all of them.
Rate the Seriousness
If the potential problems may occur, the team thinks and rates how bad it could be. They also provide each problem a score to show how serious it is. In that way, it helps them focus on the most important problems.
Decide Likelihood
Now, the team figures out how likely each problem is to happen. The team will use a rating to estimate the chances of it occurring. Thus, it helps prioritize what to pay attention to.
Determine the Causes
For each problem, the team tries to figure out why it might happen. The team looks for the main reason, like why a car might break down (e.g., low oil).
Establish Preventive Methods
Having all the information, the team will brainstorm ideas to prevent these problems. At the same time, they create strategies or plans. One of the examples is checking the oil regularly to avoid a car breakdown.
Re-Assess and Improve
Finally, the team will keep an eye on things over time. Then, they make sure the preventive actions are working. If new problems happen or old ones aren't getting better, they go back to the drawing board. From there, they’ll make improvements.
Part 4. How to Use FMEA
Using Failure Mode and Effects Analysis (FMEA), you can create a safety plan to prevent problems. Here's a simple guide on how to use FMEA:
1. Gather a Team
First, gather a group of people. Your team must know the process, product, or system you want to analyze.
2. Identify Possible Problems
In this step, begin by listing all the things that could go wrong. List and identify the issues that might happen.
3. Rate the Problems
For each problem you listed, think about how bad it would be if it happened. Use a scale, like 1 to 10, where 1 is not so bad, and 10 is really, really bad. This helps you figure out which problems are the most serious.
4. Rate the Possibility
Next, estimate how likely each problem is to occur. Give each issue a possibility score.
5. Detect Causes
Try to figure out why each problem could happen. If you're worried about using expired ingredients, the cause might be that you didn't check the expiration dates.
6. Brainstorm Preventive Actions
Now, brainstorm ways to prevent these problems or make them less bad.
7. Calculate Risk Priority
Multiply the seriousness score by the likelihood score for each problem. This gives you a “Risk Priority Number” or RPN. The higher the RPN, the more urgent it is to deal with that problem.
8. Focus on High RPNs
Pay special attention to the problems with the highest RPNs. These are the ones that need the most immediate action.
9. Implement and Monitor
Put your preventive actions into practice. Keep an eye on things to see if they are working. If problems are still happening, adjust your plan and try something else.
10. Regularly Review and Improve
FMEA isn't a one-time thing. Keep reviewing and improving your plan over time. As you learn more, you can make it even better.
Part 5. Best Tool for Doing FMEA Analysis
MindOnMap is a top-tier FMEA (Failure Mode and Effects Analysis) maker. It offers a powerful and easy-to-operate platform for businesses and organizations. It is also the best tool for seeking excellence in risk management and quality improvement. With MindOnMap, you'll find a comprehensive solution designed to simplify and streamline the FMEA process. What sets MindOnMap apart as the best FMEA maker is its intuitive interface. Both beginners and professionals may enjoy using the tool. Moreover, it offers a seamless experience for teams to work together. It ensures that everyone can contribute their expertise and insights.
Now, whether you're identifying potential failure modes, assessing their impacts, etc., MindOnMap provides the guidance you need to excel. With it, you'll have the confidence to proactively address risks, enhance product quality, and optimize operational efficiency. That’s why it is a go-to choice for those committed to achieving excellence in FMEA analysis.
Secure Download
Secure Download

Further Reading
Part 6. FAQs About What is FMEA Analysis
What are the 5 steps of the FMEA process?
The 5 steps of the FMEA process are:
1. Identify possible problems.
2. Rate the seriousness of those problems.
3. Estimate how likely the problems are to occur.
4. Find the causes of these problems.
5. Develop plans to prevent or manage the problems.
What is an example of FMEA?
Let's consider an example of FMEA in the context of a car manufacturing process: First, identify potential issues like engine overheating and paint defects. Then, rate their seriousness and likelihood. Next, look for the causes, such as a faulty thermostat or human error. Now, develop plans, like design improvements and better quality control. In that way, you’ll prevent these problems and prioritize actions.
Is FMEA lean or Six Sigma?
FMEA is a tool commonly used within the Six Sigma methodology. It's not specifically a part of Lean or Six Sigma. Yet, it is often incorporated into these quality improvement approaches.
Conclusion
To conclude, you have learned the definition and types of FMEA analysis, how it works, and how to use it. Indeed, FMEA plays an essential part in enhancing product quality, reliability, and safety across industries. As organizations seek effective FMEA solutions, MindOnMap stands out as one of the best FMEA makers. With its straightforward interface and powerful features, users can ensure that they can make their desired FMEA diagram.